Get inspired: Vandersanden
'Green' facing bricks thanks to carbonation.
The new Pirrouet® plant owned by brick manufacturer Vandersanden was opened on 18 September 2024. The carbon-negative Pirrouet facing bricks were launched on the market in October 2023 and ‘with the opening of this new plant, we can now produce them on a large scale,’ says Vandersanden CEO Johan Deburchgrave. ‘This is not just a pilot project, but an essential and next serious step towards sustainable production and reduction of CO2 emissions.’
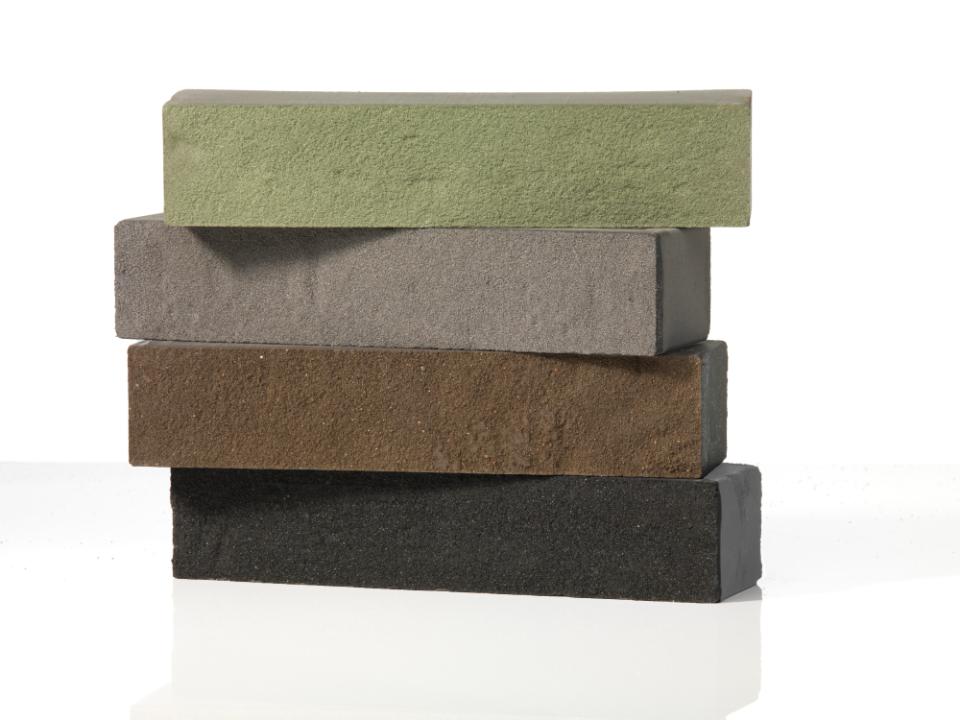
CEO Johan Deburchgrave makes a case for offering the first carbon-negative facing brick for use in construction worldwide. The green electricity that powers the plant is largely generated by its own solar panels and a wind turbine. The heat needed for the drying process is residual heat from nearby brick kilns. Vandersanden obtains the CO2 needed for the brick manufacturing process from surpluses from the ports of Antwerp and Ghent.
Pirrouet® carbon-negative bricks absorb CO2 during the production process rather than emitting it. They are made using around 80% residual products from the steel industry, and use of carbonation technology permanently stores CO2 in the bricks. Moreover, that carbonation process continues for some time after the production process is complete. The net CO2 storage by these bricks exceeds the emissions. Vandersanden is currently developing a circular dry-stacking system for these Pirrouet® facing bricks that will allow the bricks to be removed at the end of a building’s or house's lifecycle and reused. Another great example of circularity is that up to 80% use is made of secondary raw materials. In addition to circularity, a smaller waste mountain also offers a new perspective on resource policy and pollution from waste streams.
The carbonation technology was developed by VITO and Orbix. Using this new technology, a range of products can be developed which have the same technical properties as conventional (building) products but with much lower environmental impact.
Carbonatatie
Orbix, a company that processes waste from steel mills, discovered back in the 1990s that a part of that residual waste was transformed in a reaction with CO2 into a very hard material, which can be used in construction. Vandersanden further developed the process, known as carbonation, to turn that raw material into facing bricks.
The facing bricks are no longer fired in energy-consuming brick kilns, but are formed using carbonation. But what exactly is that? Carbonation is a natural process in which materials containing calcium (Ca) react with carbon dioxide (CO2) to form calcium carbonate (CaCO3). Calcium carbonate occurs naturally in rocks all over the world, and is a major source of natural CO2 storage. The fine residue left over from steel production is converted by adding CO2 to high-grade building materials. The carbonates formed in this process provide a hard limestone-like bond to the whole compound.
VITO as a partner
The technology behind the Pirrouet® bricks was facilitated in partnership with VITO. VITO is an independent Flemish research organisation specialising in cleantech and sustainable development, with the aim of accelerating the transition to a sustainable world. To this end, VITO works on projects worldwide that have an impact in the pursuit of a society where sustainability is the norm. They develop innovative technological solutions and actively share their knowledge with companies and governments.
To maximise their impact, VITO focuses on three impact areas: sustainable resource economy; climate adaptation and mitigation; and sustainable living environment. VITO has an extensive laboratory for testing concrete and other building materials, designed and assembled in-house at VITO. This makes it possible to study every conceivable aspect of building materials.
From technology to industry
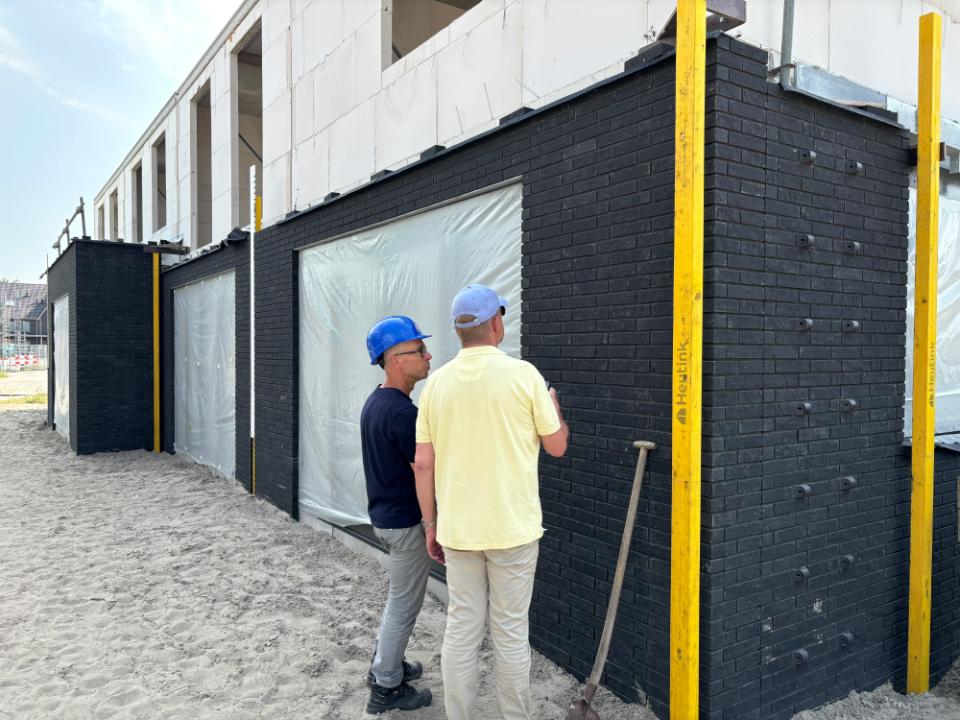
Vandersanden, which celebrates 100 years as a business next year, is the largest family-owned brick manufacturer in Europe. The company employs over 850 staff at ten production sites in Belgium, the Netherlands, France, Germany and the UK. The company can produce more than 550 million bricks per year. The carbon-negative facing brick fits in with the 'Together to Zero' strategy, which aims to achieve carbon-neutrality by 2050.
Every tonne of Pirrouet® bricks absorbs 60 kg of CO2. For the present, production of these bricks is limited, with the 20 million bricks produced annually making up only 4 per cent of the approximately 550 million facing bricks and pavers produced by Vandersanden every year. However, the company has plans to double production rapidly if the Pirrouet® carbon-negative facing brick, with its unique aesthetic appearance, proves popular with customers.
In the meantime, the bricks have already been supplied to three projects: the Living Tomorrow innovation centre in Vilvoorde, in Belgium, a 60-home development project in Almere, the Netherlands, and the new Colruyt supermarket in the Belgian town of Temse.
Like to know more about circular business?
Disclaimer:
Unless expressly provided otherwise, all information that you consult or obtain here has a non-binding and purely informational value. It is updated to the best of our ability and at regular intervals. However, KBC Bank NV gives no guarantees as to the topicality, accuracy, correctness, completeness or suitability for a particular purpose of this information. The information provided here does not constitute advice or an offer to sell products or services and is not intended for commercial use. You remain fully responsible for the consequences of the use you make of this information. The intellectual property rights to the information, publications and data provided here belong to KBC Bank NV or third parties and you must refrain from any infringement thereof. Except with the express prior and written consent of KBC Bank NV, any transfer, sale, distribution or reproduction of this information is prohibited.